The Impact of Steel Coil Packaging on Cold Rolling Production Efficiency
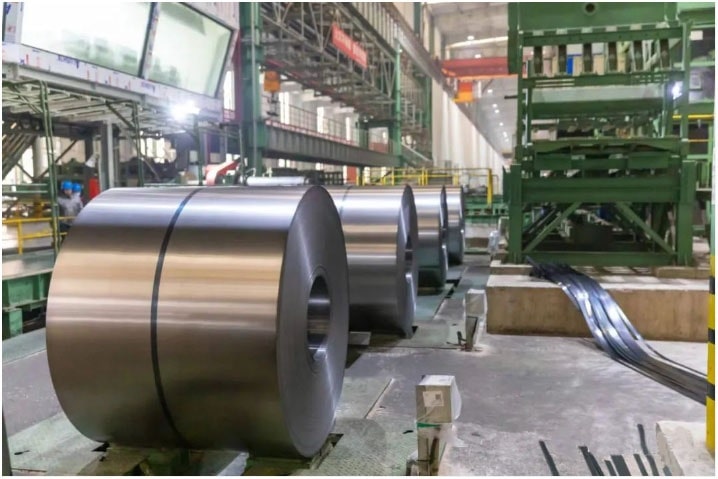
Cold-rolled sheets (including: electrical steel plates, stainless steel plates, color plates, galvanized sheets, etc.) are usually supplied in the form of plates cut into certain specifications, or in coiled strips (collectively referred to as plates and strips).
In recent years, due to changes in steel sales channels, the original end-user purchasing model has changed from purchasing directly from steel plants to purchasing through steel markets (steel distribution centers). In this way, the plates required by users can be cut at the steel distribution center, and the steel mill can meet most requirements as long as it provides steel coils. The direct benefits of this change are: reduced product specifications and improved production efficiency. It is precisely because of the increase in strips that steel coil packaging accounts for an increasing proportion of the entire steel packaging. Therefore, it is very important to study the impact of steel coil packaging on cold rolling production efficiency and product quality.
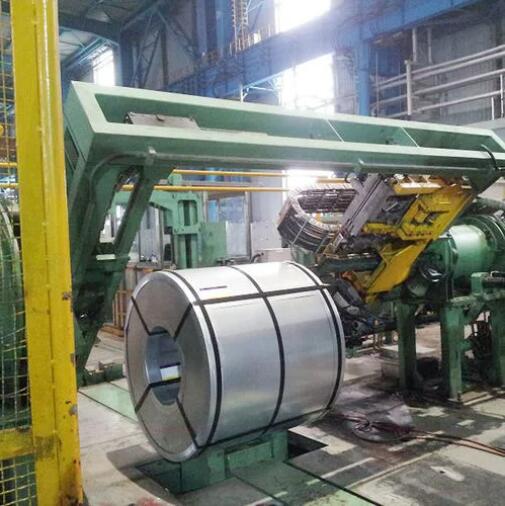
According to the process flow of cold rolling production, packaging is the last process in the finishing workshop (or “post-processing workshop”), most commonly located behind the “rewinding and slitting unit”. If it is manual packaging, a packaging area will be set up. If it is mechanical packaging, there will be a packaging unit. As we all know, the production speed of cold-rolled sheet is very fast and it is a highly automated production process. Therefore, all supporting equipment, whether host or auxiliary, must meet the production speed requirements under the premise of ensuring quality, which has become the most important parameter of process design.
Taking the cold rolling project with an annual output of 1.3 million tons as an example, the calculation results of the speed to meet this production requirement are given:
- Output: 1.3 million tons/year;
- Annual working hours: 6600h (three shifts continuous work system);
- Steel coil weight 3 – 15 t;
- Average roll weight 5 t;
- The number of circumferential straps is 3 to 5;
- The number of eye straps is 4 to 6;
- Production speed 1. 523 minutes/roll.
In China, because many steel companies did not have cold rolling plants before, the last process of the product – packaging, is often ignored in newly built cold rolling projects. It is mistakenly believed that China’s labor force is cheap and manual packaging can be used. This incorrect understanding has led to the very low level of steel coil packaging technology possessed by many companies that are building cold rolling projects. The design concept of “emphasis on main work and light on auxiliary work” has set up a “bottleneck” for the overall production capacity after the project is put into operation.
However, we are also very lucky to see that in recent years, through exchanges with foreign steel companies, decision-makers of Chinese steel companies have begun to realize the importance of steel coil packaging in ensuring safe storage and transportation, improving production efficiency, and improving product quality. Increasingly, More and more companies are constructing packaging units as important auxiliary process equipment in new cold rolling production lines, and the degree of automation of the equipment has also been significantly improved.
Tags: Automatic coil packing line for slit steel coils and copper coils, steel strip coil wrapper machine, Upender and tilter
Recent Comments